Rosehill Industrial Estate, Carlisle (Phase 1)
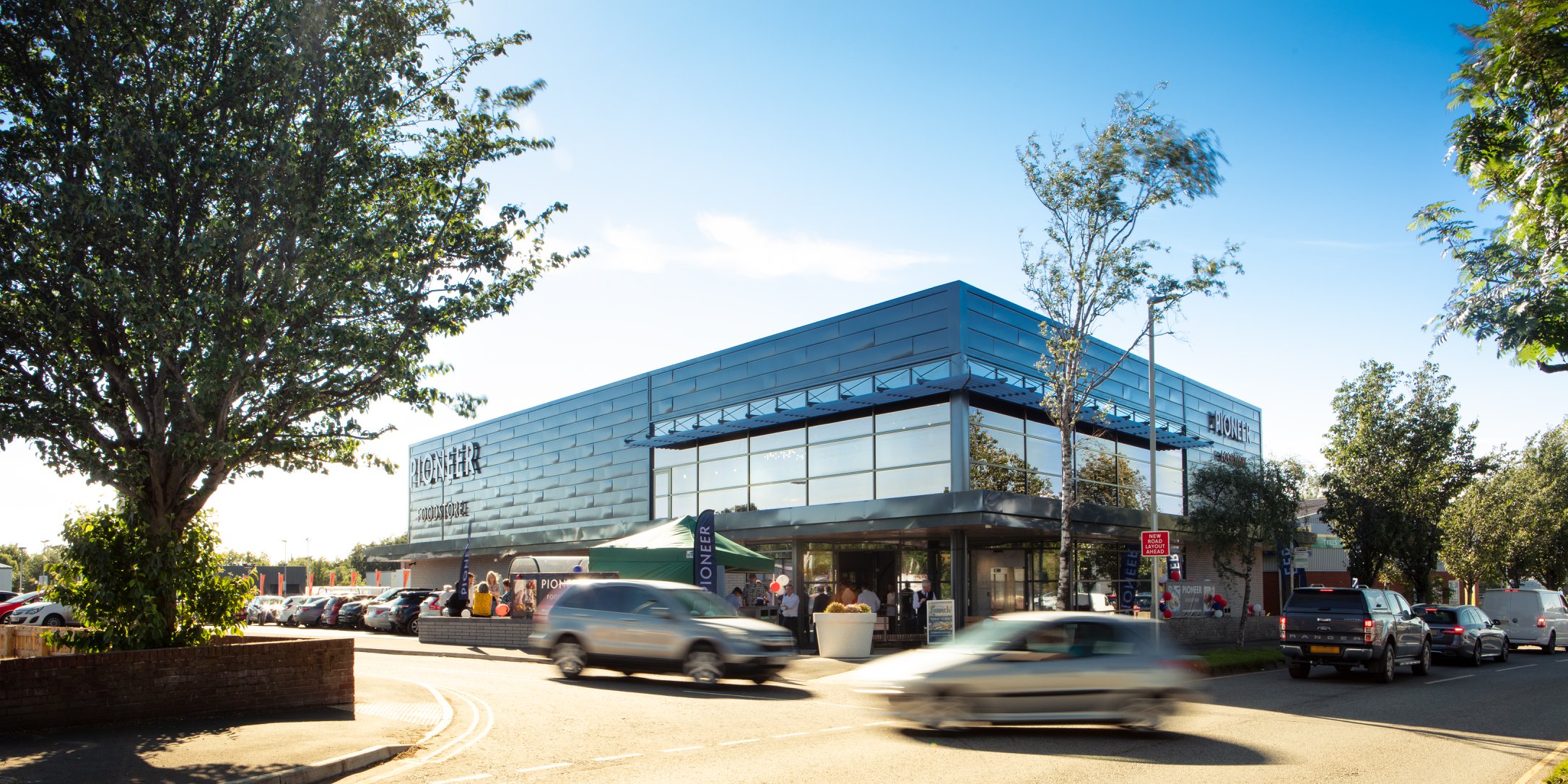
What We Delivered at Rosehill Industrial Estate, Carlisle – Phase 1
Thomas Armstrong (Construction) Ltd was appointed to carry out the design and construction of three new industrial/trade counter units as part of a phased development at Rosehill Industrial Estate in Carlisle.
This project included the construction of steel portal frame buildings with traditional facing brickwork and profiled cladding above. Each unit was completed to shell standard with service connections, ready for tenant fit-out. The units were constructed with flexibility in mind to support future tenant needs and uses.
External works included large concrete service yards, permeable block paving to car parks, road surfacing and new boundary treatments. All works were delivered in accordance with the latest planning and building regulation requirements, with strong coordination between the design team, structural engineers and subcontractors.
Works Included:
- Design and construction of 3 light industrial units
- Steel portal frame structure with facing brick and profiled cladding
- Precast concrete floors and insulated composite roof panels
- Installation of service ducts and capped utilities to each unit
- Formation of reinforced concrete service yard
- Permeable block paving to car park areas
- Tarmac surfacing, fencing and boundary works
- Landscaping and lighting installations
- Coordination with consultants and structural engineer throughout
Project Achievements:
- Delivered on time and within programme
- Flexible, high-quality space provided for multiple tenant types
- Compliant with all relevant planning, building and fire safety regulations
- Strong collaboration with client and design team
- Set the foundation for future phases of industrial estate development
Explore More of Our Work
Discover other projects we’ve successfully delivered across the region — from commercial builds and civil engineering schemes to bespoke joinery and residential developments.